Application of melt filter in chemical fiber production
With the progress of society and the development of science and technology, people's quality requirements are constantly improving. Quality is the foundation for the survival of enterprises. Improving quality and reducing costs is the pursuit of every enterprise. Therefore, many enterprises are constantly upgrading and innovating, improving product quality and reducing costs.
In the melt spinning forming process, improve the spinning quality, reduce the cost of spinning, melt pump filter is an essential device, because the spun filament diameter is small, the spinneret hole is very small, the melt mixed with any impurities or gel particles are not allowed, so improve the purity of melt pump melt is one of the key normal spinning and finished yarn quality. So the high speed spinning melt pump must be installed pre filter, in order to improve the purity of the melt, reduce the filtration layer component in spinning burden, prolong the service cycle, reduce due to change of the spinning components of waste that improve the quality and reduce the cost.
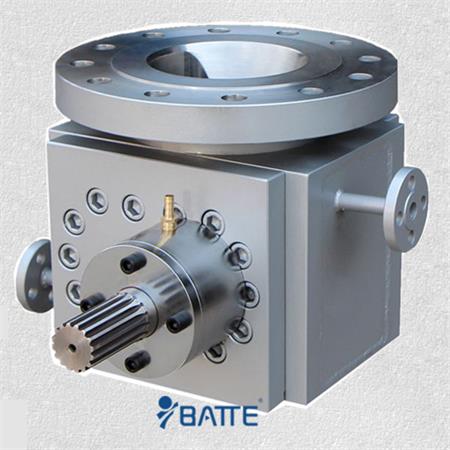
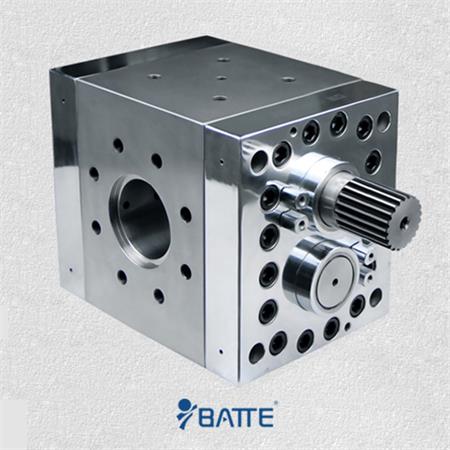
In the device prefilter, we must select the right melt pump filter, which is not easy to plug, withstand voltage, resist temperature and corrosion, and adapt to the continuous spinning requirements. Using a double cylinder filter, the operation can be switched continuously, and the fluctuation can be reduced as much as possible when the switch is switched.
Based on the above issues, the melt pump filter for continuous filtration of chemical polymer filter double cylinder continuous switching used for high polymer melt, to remove impurities in the melt and melting of the gel particles, improve the spinning performance and ensure quality in high speed spinning, spinning, spinning fine denier yarn spinning and recycled materials, are indispensable to prolong the life of spinning equipment, improve equipment utilization rate and increase the yield plays an obvious role.With the progress of society and the development of science and technology, people's quality requirements are constantly improving. Quality is the foundation for the survival of enterprises. Improving quality and reducing costs is the pursuit of every enterprise. Therefore, many enterprises are constantly upgrading and innovating, improving product quality and reducing costs.
In the melt spinning forming process, improve the spinning quality, reduce the cost of spinning, melt pump filter is an essential device, because the spun filament diameter is small, the spinneret hole is very small, the melt mixed with any impurities or gel particles are not allowed, so improve the purity of melt pump melt is one of the key normal spinning and finished yarn quality. So the high speed spinning melt pump must be installed pre filter, in order to improve the purity of the melt, reduce the filtration layer component in spinning burden, prolong the service cycle, reduce due to change of the spinning components of waste that improve the quality and reduce the cost.
In the device prefilter, we must select the right melt pump filter, which is not easy to plug, withstand voltage, resist temperature and corrosion, and adapt to the continuous spinning requirements. Using a double cylinder filter, the operation can be switched continuously, and the fluctuation can be reduced as much as possible when the switch is switched.
Based on the above issues, the melt pump filter for continuous filtration of chemical polymer filter double cylinder continuous switching used for high polymer melt, to remove impurities in the melt and melting of the gel particles, improve the spinning performance and ensure quality in high speed spinning, spinning, spinning fine denier yarn spinning and recycled materials, are indispensable to prolong the life of spinning equipment, improve equipment utilization rate and increase the yield plays an obvious role.